Glass has long been celebrated in architecture and construction for its aesthetic appeal and versatility. From the towering glass facades of skyscrapers to the delicate panes in residential windows, glass serves both functional and decorative purposes. Its transparency allows for natural light penetration, reducing energy costs and enhancing occupant well-being. Moreover, modern advancements have bolstered glass’s reputation as one of the most durable building materials available. However, despite its robustness, glass is not impervious to degradation. Under certain environmental conditions, glass can experience staining and corrosion, compromising its appearance and functionality.
Glass corrosion is a chemical process where the components of glass react with water or other chemicals, leading to the formation of residues or stains on its surface. This phenomenon not only affects the optical clarity of the glass but can also weaken its structural integrity over time. Understanding the causes and mechanisms of glass corrosion is essential for architects, builders, and facility managers to implement effective preventive measures.
This article delves into the significant causes of glass corrosion in the construction industry and outlines practical strategies to prevent it, ensuring the longevity and performance of glass installations.
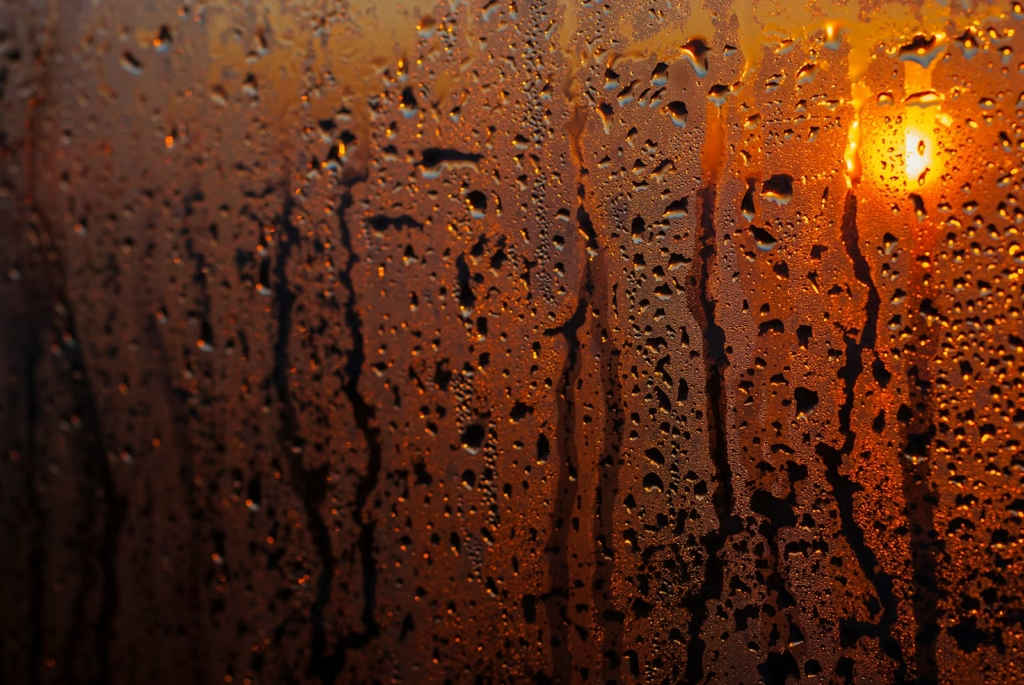
Causes of Glass Corrosion
Extended Exposure to Water or Chemicals
At its core, glass corrosion is a result of prolonged exposure to water or chemical agents that initiate chemical reactions on the glass surface. Most commercial glass used in construction is soda-lime-silica glass, composed primarily of silicon dioxide (SiO₂), sodium oxide (Na₂O), and calcium oxide (CaO). When water comes into contact with this type of glass, it can slowly react with these components, leading to corrosion or staining.
For instance, rainwater, condensation, or high humidity levels can facilitate the interaction between water molecules and the glass surface. While the reactions are often subtle and occur over extended periods, the cumulative effect can be significant, especially in environments where the glass is consistently exposed to moisture.
Stages of Glass Corrosion
The corrosion of glass typically progresses through two primary stages, each characterized by specific chemical reactions and effects on the glass surface.
Stage 1 Reaction
In the initial phase, known as Stage 1 corrosion, a diffusion-controlled ion-exchange process occurs. Here’s how it unfolds:
- Ion Exchange: Sodium ions (Na⁺) present in the glass matrix are replaced by hydrogen ions (H⁺) from the water. This exchange is facilitated by the diffusion of ions across the glass-water interface.
- Leaching Process: As sodium ions migrate into the water, they leave behind vacancies in the glass structure. This leaching process increases the concentration of sodium ions in the water layer adjacent to the glass surface.
- pH Increase: The accumulation of sodium ions in the water layer leads to the formation of sodium hydroxide (NaOH), raising the pH level of the surface environment. Typically, the pH can rise up to 9 during Stage 1.
- Surface Alkalinity: The elevated pH indicates higher alkalinity, which can initiate further reactions. However, during this stage, the optical quality and surface integrity of the glass remain largely unaffected.
It’s important to note that Stage 1 corrosion can go unnoticed because the glass maintains its clarity and strength. Nevertheless, the chemical groundwork is being laid for more severe corrosion if the conditions persist.
Stage 2 Reaction
Stage 2 corrosion commences when the pH level at the glass surface exceeds 9. At this point, the environment becomes sufficiently alkaline to attack the silicate network of the glass:
- Silicate Network Attack: The high pH environment causes hydroxide ions (OH⁻) to break the silicon-oxygen bonds in the glass structure. This attack leads to the dissolution of the glass network at a microscopic level.
- Microscopic Pitting: Initial signs of Stage 2 corrosion include tiny pits or craters on the glass surface, observable under magnification. These pits are sites where the glass structure has been compromised.
- Surface Damage: As the corrosion progresses, the surface damage becomes more pronounced. The glass may develop haze, cloudiness, or iridescent stains, affecting its optical clarity.
- Impact on Optical Quality: While the structural integrity of the glass may remain intact during Stage 2, the degradation of optical properties can be significant, necessitating replacement in applications where clarity is essential.
Atmospheric Effects
In addition to water-induced corrosion, atmospheric gases play a role in glass degradation:
- Carbon Dioxide Interaction: Atmospheric carbon dioxide (CO₂) can dissolve in the thin layer of water on the glass surface, forming carbonic acid (H₂CO₃). This weak acid can react with sodium and calcium ions leached from the glass.
- Formation of Carbonates: The reactions result in the formation of sodium carbonate (Na₂CO₃) and calcium carbonate (CaCO₃) residues on the glass surface. These compounds manifest as whitish or hazy stains, further compromising the glass’s appearance.
- Environmental Pollutants: Other atmospheric pollutants, such as sulfur dioxide (SO₂) and nitrogen oxides (NOₓ), can contribute to glass corrosion, especially in urban or industrial areas with high levels of air pollution.
Prevention of Glass Corrosion
Preventing glass corrosion is a multifaceted endeavor that involves proper handling, cleaning, storage, and material selection. Implementing the following strategies can significantly reduce the risk of corrosion and extend the life of glass installations.
Proper Cleaning and Drying
- Regular Maintenance: Establish a routine cleaning schedule to remove contaminants before they can initiate corrosion processes. Use clean, soft cloths or squeegees to wipe down glass surfaces.
- Drying Surfaces: After cleaning, ensure that glass surfaces are thoroughly dried. Standing water or residual moisture can accelerate corrosion reactions.
- Water Quality: Use purified or deionized water for cleaning when possible. Tap water may contain minerals and chemicals that contribute to staining and corrosion.
Avoiding Improper Cleaning Practices
- Chemical Cleaners: Steer clear of harsh chemical cleaners, especially those containing acids or alkalis that can etch or damage the glass surface.
- Abrasive Materials: Do not use abrasive scrubbers or cleaning pads that can scratch the glass, creating sites for corrosion to initiate.
- Manufacturer Guidelines: Follow the glass manufacturer’s recommendations for cleaning products and techniques to prevent voiding warranties or causing unintended damage.
Protective Measures During Shipping and Handling
- Interleaving Materials: When storing or transporting glass, use paper or powdered interleaving materials between glass panes. These materials serve multiple purposes:
- Abrasion Prevention: They act as a cushion to prevent mechanical damage and scratching during movement.
- Moisture Absorption: Some interleaving materials can absorb moisture, reducing the amount of water in contact with the glass surface.
- pH Control: Certain interleaving powders are formulated to neutralize alkali buildup, maintaining a balanced pH and inhibiting Stage 1 corrosion processes.
- Environmental Controls: Store glass in climate-controlled environments where humidity and temperature are regulated. Avoid exposure to rain, condensation, or drastic temperature fluctuations.
Selecting Suitable Glass for Applications
- Assessing Environmental Conditions: Before selecting glass for a project, evaluate the environmental conditions it will face, including humidity levels, exposure to pollutants, and proximity to corrosive substances.
- Specialized Glass Types:
- Anti-Corrosive Glass: For high-humidity environments like bathrooms, swimming pools, or coastal areas, consider using glass treated with anti-corrosive coatings. These coatings create a barrier that resists moisture penetration and chemical attack.
- Low-Iron Glass: Low-iron glass has reduced impurities that can react with environmental agents, making it less prone to staining and corrosion.
- Tempered or Laminated Glass: These types offer enhanced durability and may come with protective interlayers that reduce the risk of corrosion.
- Protective Coatings: Apply hydrophobic or oleophobic coatings that repel water and oils, minimizing contact between the glass surface and corrosive agents.
Additional Preventive Strategies
- Design Considerations: Incorporate design elements that minimize water retention on glass surfaces, such as overhangs, drip edges, or inclined glass installations that facilitate water runoff.
- Ventilation: Ensure adequate ventilation in enclosed spaces to reduce humidity levels and prevent condensation on glass surfaces.
- Regular Inspections: Conduct periodic inspections of glass installations to identify early signs of corrosion or staining, allowing for timely intervention.
Conclusion
Glass corrosion poses a significant challenge in the architecture and construction industries, potentially affecting both the aesthetic and functional aspects of glass installations. By understanding the chemical processes that lead to corrosion and recognizing the environmental factors that contribute to it, stakeholders can implement effective preventive measures.
Proper cleaning and maintenance, careful handling and storage, and the selection of appropriate glass types are critical steps in mitigating corrosion risks. Additionally, employing protective coatings and design strategies that reduce exposure to corrosive agents can enhance the longevity of glass structures.
Ultimately, proactive management of glass corrosion not only preserves the visual appeal of buildings but also ensures the safety and satisfaction of occupants. As the industry continues to innovate, embracing best practices for glass care will remain essential for sustainable and resilient architectural designs.